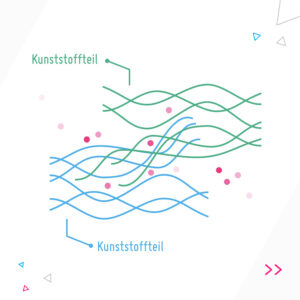
Solvent bonding
Solvent bonding allows thermoplastics to be bonded permanently without any heat source and without any adhesive remaining. In this short and more technical article, we look at how it works, suitable solvents and the advantages of this technique.